Vibration Monitoring for Cooling Towers
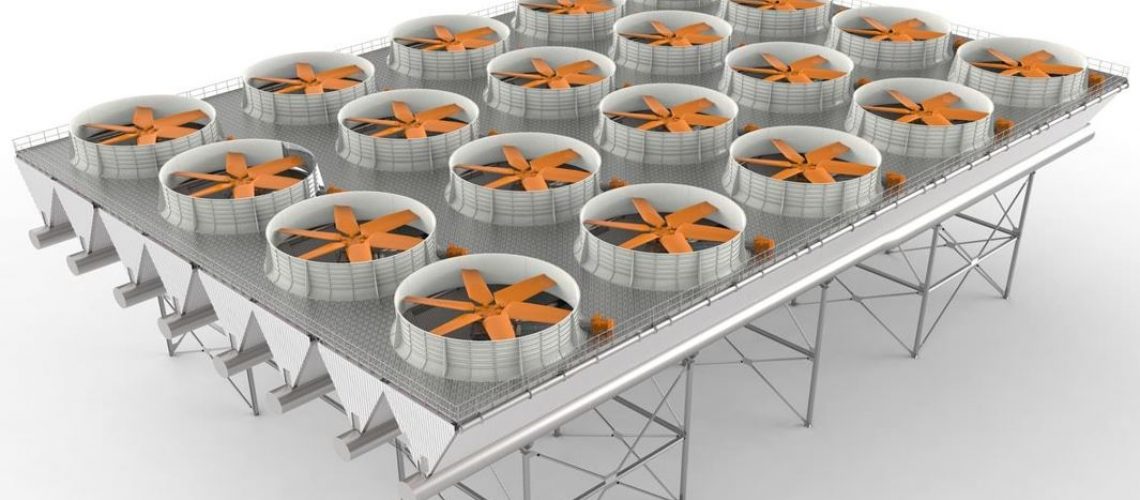
Vibration Monitoring for Cooling Towers
Article by I-care
Cooling towers are a logical choice for vibration monitoring. Due to their often critical role in maintaining operational efficiencies. We use vibration analysis to improve reliability and extend the lifetime of cooling tower equipment.
How It Works
The machinery generally consists of three phases: motor, gearbox, and fan. Typically we install vibration sensors on the bearing surface in either the horizontal, vertical, or axial directions.
What We Offer
4.0 Solution With Wi-care 200
Using the Wi-care 200 hard- and software we can connect all types of sensors. These can vary from dynamic accelerometers to temperature-, pressure-, distance-, oil-, windspeed-,… sensors. In this way we can accurately predict failures using 4.0 algoritmes that combines all data.